We know that Tesla vehicles use a DC lithium-ion battery. So, why does Tesla use 3-phase AC induction motors instead of DC motors?
Tesla uses AC induction motors because it has more torque even at high speed, simple design, cost-effective, do not need rare earth minerals rich permanent magnet, high reliability, and easier regenerative braking system design.
Let’s elaborate.
In this article, we will explain everything in simple language so that everyone can understand.
There are various types of motors such as DC motor, Brushless DC motor (BLDC), AC induction motors, stepper motor, etc.
Brushed DC motor:
The following picture shows a simplified internal diagram of a brushed DC motor. Most household electronics use this type of DC motor, such as toys, electric toothbrushes, razors, etc.
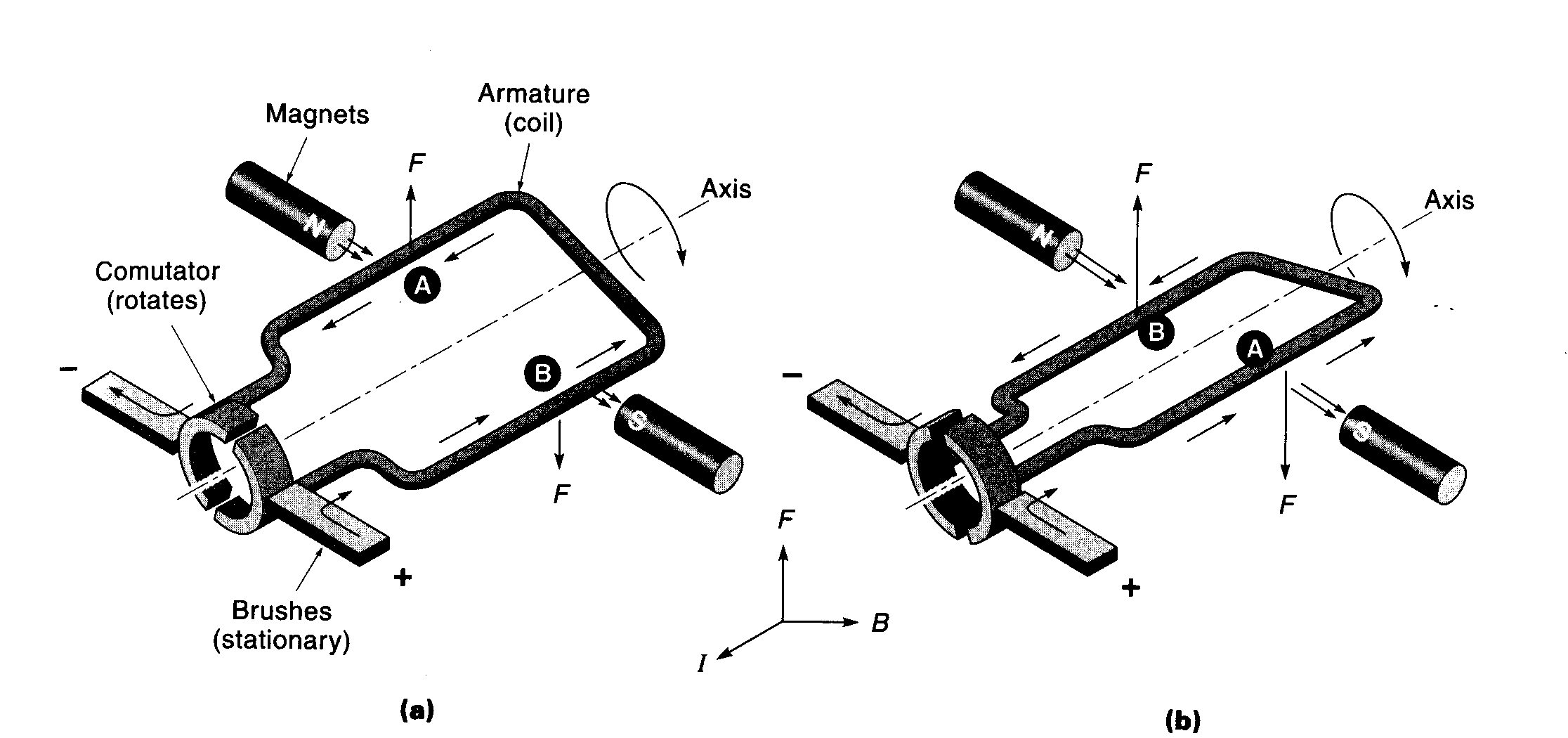
If you look closely at the above picture, you will see that the middle rotating part (rotor) is directly connected to electricity through a metal contact. Due to friction, this part wears out over time. Therefore, after a few hundred hours of operation, these motors fail and need the contactor replacement.
Furthermore, if the controller fails, it can either open or short the motor coil. A shorted coil would lead to a runaway situation.
So, for an electric vehicle, brushed DC motors are not a wise choice.
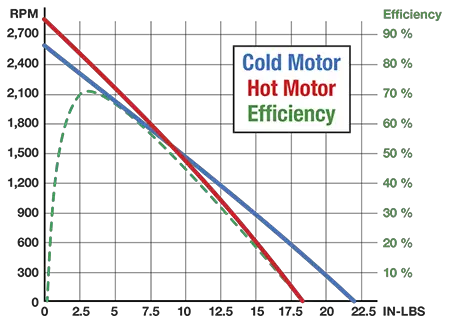
Brushless DC motor performance:
The Brushless DC (BLDC) motor has a high initial starting torque; however, its performance or efficiency decreases linearly with speed increase.
If an electric vehicle uses a BLDC motor, the car will use significant electrical energy on the highway speed. Furthermore, at high speed, your vehicle would respond slower to your accelerator input.
The Toyota Prius has a bad reputation that it can’t accelerate fast enough. The primary reason for the slow acceleration is that Toyota uses DC brushless motors in the Prius lineup.
Before Tesla, everyone used to bash electric vehicles for their slow performance. The slow speed of these EVs is also related to DC motors.
Rare Earth minerals:
To make a good DC motor, we need strong permanent magnets. We need rare earth minerals to produce these strong permanent magnets.
Before the 1980s, the US had rare earth element industries, especially in California. However, in the 1980s, most of these companies moved to China for lower labor costs and environmental restrictions. Over the next two decades, the US has driven out most of these companies out of business or forced them to move to China through strict environmental laws.[1]
Since then, China controls more than 90% of refined rare earth minerals in the world.
Elon Musk knew that when a single country controls an essential element for a product with no alternative, it could become a bottleneck for future car production. It’s similar to OPEC and how they manipulate the oil price.
In 2010, it became clear that Elon made the right choice by not using the DC motor, which uses rare earth elements. That year, China banned the export of rare minerals to Japan over a diplomatic dispute and tried to crush their economy. As a result, companies in other countries started stockpiling rare minerals to secure supply. It led to a massive price spike.
Therefore, DC motors are not the right choice when a company that targets to build millions of cars each year.
Rare minerals refinery:
China is not as strict as the US on environmental regulations. During the 1990s, the US put various strict laws on rare minerals refineries. It’s because, without proper procedure, these refineries have long-lasting effects on groundwater and the environment.
Elon knew that we couldn’t move into a sustainable future if we keep polluting the earth in the process. On Tesla’s part, it was a good move.
Side Note: Both the Brushless DC motor and AC induction motors need a converter. Any energy loss due to the converter, therefore, the same for both types of motors.
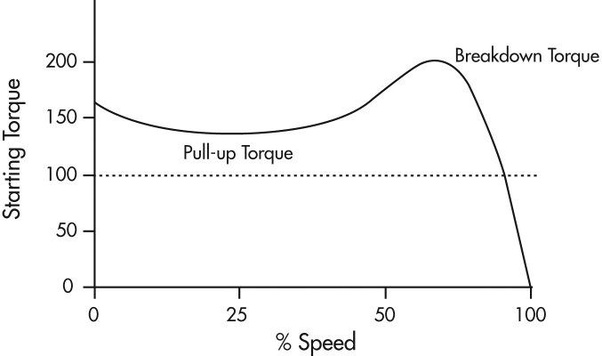
Benefits of an AC induction motor:
Previously we have seen that the DC motor’s efficiency decreases linearly as speed increases. While the AC induction motors have slight torque reduction, DC motors have a fast falloff.
The advantage of the AC induction motor is its torque property is very close to the ideal characteristic. This motor’s torque is constant up to a certain speed and then decreases, unlike the DC motor.
The induction motor does not have permanent magnets, no brushes, no commutator rings, no position sensors. Its design is simple and has a rugged construction.
The brushless DC (BLDC) motor has permanent magnets in the rotor. As those permanent magnets in the rotor rotate relative to the stator, they produce eddy currents in the stator metal and wiring. With increasing RPM, eddy currents dissipate more power, decreasing efficiency. On a highway, an EV that uses a BLDC motor is less efficient than an EV with an AC induction motor.
Another benefit of the Induction motor is the easier and simple regenerative braking system design. In the case of the DC motor, the system is very complicated compared to an induction motor.
AC induction motors have another benefit. This motor uses winding coils in the rotor. Due to the operating principle, the current flowing through this coil produces a stronger magnetic field than permanent magnets. Therefore, an induction motor can generate more peak power than a brushless DC motor.
If we need more torque in an induction motor, we can achieve it by increasing the magnetic field strength (B), especially at low speed. Likewise, we need to reduce the B field at a low torque level to minimize loss due to eddy current and hysteresis.
There’s no easy way to change the magnetic field strength (B) in a permanent magnet DC brushless motor. In contrast, the B field is adjustable in an AC induction motor.
Moreover, though Induction Motor (IM) is slightly less efficient than permanent magnet DC motors (88% vs. 95% depending on various factors), the overall cost-benefit for AC induction motor is more.
In Short, Induction motors have –
- Simplified design.
- Lower cost.
- Fewer parts.
- Higher reliability.
- More efficient at highway speed.
- No rare earth minerals thus reliable production cost.
Drawbacks of AC induction motor:
There are several drawbacks of AC induction motors.
- A BLDC motor generates less heat, but an induction motor generates more heat due to eddy current and hysteresis. So, active cooling is required.
- BLDC controllers are easier to design than induction motors.
Side Note:
Tesla Model 3 uses permanent magnet (PM) motors instead of the AC induction motor. There are several reasons for this choice.
Tesla calls its Model 3 motor as Permanent Magnet Switched Reluctance Motor (PMSRM). It’s a new type of motor that Tesla uses and different from any other motors available in the market.
The PMSR motor that Model 3 has produces up to 450 horsepower. It is one of the lightest and smallest motors for its output. Only a gas turbine has a similar output efficiency in the same form factor.
Model 3 is a smaller vehicle than Model S and Model X. The permanent magnet motor minimizes the motor’s size and weight while not compromising Tesla’s performance and efficiency specification.
It’s a balance between motor cost, efficiency, battery cost, and the vehicle range.
Bottom Line:
Everything has pros and cons. When we compare AC induction vs. DC motors’ pros and cons, it’s evident that AC induction motors have more benefits from the product supply chain to motor efficiency over DC motors. In conclusion, Tesla made a great decision early on by choosing AC induction motors over DC motors for their vehicle.
Tesla Blog: